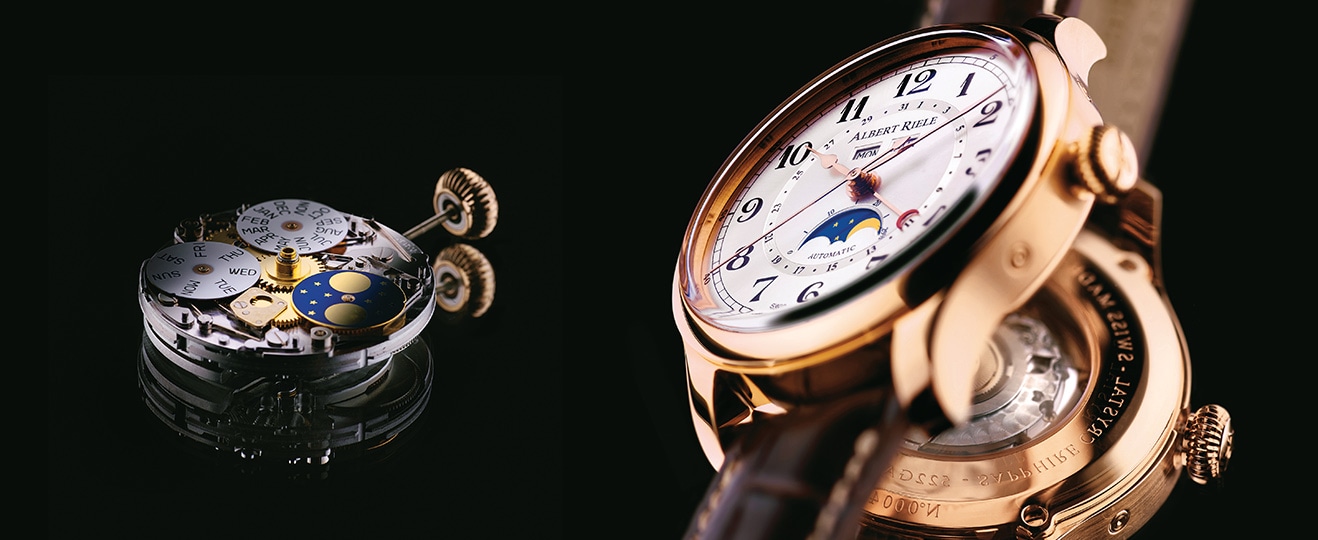
Budowa zegarka
- MECHANIZM – urządzenie odmierzające czas wykorzystując zjawiska elektryczne lub zjawiska mechaniczne; więcej informacji nt. mechanizmów można znaleźć w części poświęconej mechanizmom;
- KOPERTA – część zegarka, w której umieszczony jest mechanizm, koperta może mieć różne kształty;
- SZKŁO – przezroczysty element, przez który widoczna jest tarcza wraz ze wskazówkami; niekiedy szkło montowane jest także w deklu, dzięki czemu widoczna jest praca mechanizmu;
- TARCZA – umieszczone są na niej m.in. oznaczenia godzin i minut (np. indeksy) może być otwarta, co umożliwia obserwację praca mechanizmu;
- INDEKSY – najczęściej cyfry rzymskie lub arabskie, bądź kropki lub kreski, w miejscach na tarczy odpowiadający poszczególnym godzinom;
- KORONKA – „pokrętło" znajdujące się najczęściej z prawej strony koperty, na godzinie trzeciej; za jej pomocą możliwa jest min. zmiana położenia wskazówek (ustawienie prawidłowej godziny lub daty) oraz nakręcenie zegarka w przypadku mechanizmów mechanicznych;
- RAMKA (LUNETA, PIERŚCIEŃ) – element otaczający szkło na kopercie, zwykle w tym samym kształcie, co koperta; pełni funkcje ozdobne oraz, niekiedy, wskazań (np. tachometr); pierścień może być obrotowy;
- DEKIEL – spodnia część zegarka, na której umieszczone są opisy producenta (np. nr. referencyjny, seryjny, informacje o wodoszczelności itp.) Dekiel zamyka kopertę i zabezpiecza jego mechanizm przed uszkodzeniami. Może posiadać szkło, przez które widoczna jest praca mechanizmu;
- WSKAZÓWKI – są to wskaźniki zamontowane na obracających się w mechanizmie kołach; poruszając się nad tarczą wskazują np. godzinę, datę;
- BRANSOLETA lub PASEK.
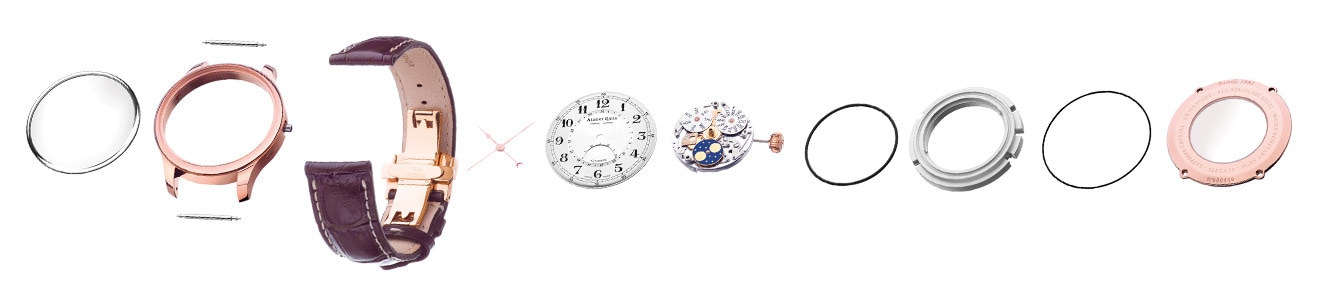
Materiały wykorzystywane do produkcji kopert i bransolet
Metale szlachetne – bardzo eleganckie, prestiżowe, jednocześnie są rzadko używane ze względu na wysokie koszty:
Platyna – ciężki srebrzystobiały metal, w stanie czystym dość kowalny i ciągliwy, nie ulega utlenianiu w powietrzu, jest również odporna na działanie kwasów, także kwasu solnego,
– żółte i białe złoto – łatwo podlegające obróbce, stopy mają zróżnicowane kształty, twardość oraz kolor;
Stal – stopy stali wysokiej jakości, trwałe i odporne;
Tytan – materiał bardzo odporny na korozję, jest hipoalergiczny – to jego istotna zaleta. Ma też dużą odporność mechaniczną w stosunku do swojego własnego ciężaru, jest niemal tak wytrzymały, jak stal. Jednakże na skutek kontaktu np. z ubraniem, bądź innymi powierzchniami, może dochodzić do jego wybłyszczania lub porysowania. Najczęściej występuje w kolorze ciemnej szarości;
Zalium – stop glinu i cyrkonu, opatrzony znakiem towarowym Harry Winston. Jest to ultralekki, hipoalergiczny materiał o wysokiej wytrzymałości;
Spieki ceramiczne – nowoczesny materiał o wysokiej twardości i odporności na zarysowania; jednakże pod wpływem bodźców mechanicznych może ulec uszkodzeniu;
Mosiądz i jemu podobne stopy metali kolorowych – łatwe w obróbce, o średniej i niskiej odporności na korozję i bodźce mechaniczne;
Stopy metali lekkich – niska odporność na korozję i bodźce mechaniczne;
Tworzywa sztuczne – materiał z reguły tani, o zróżnicowanej wytrzymałości, łatwo poddający się obróbce.
Materiały wykorzystywane do produkcji pasków
Skóra – cielęca albo egzotyczna, np. strusia, krokodyla, aligatora, węża;
Kauczuk – ostatnio bardzo modny, nie tylko w zegarkach sportowych;
Inne tworzywa – np. guma, silikon, stosowane głównie w zegarkach sportowych.
Materiały wykorzystywane do produkcji szkieł zegarków.
Hesalit – utwardzony i oczyszczony chemicznie polipropylen (plastik). Dawniej używane były w zegarkach wyższej klasy, dziś już rzadko. Twardość w skali Mohsa wynosi ok. 1 B. Niska odporność na zarysowania;
Szkła mineralne – dobrej jakości szkła na bazie krzemu, używane przede wszystkim w klasycznych zegarkach średniej klasy. Twardość w skali Mohsa: 4 do 5. Odporność na zarysowania na poziomie średnim. Stosuje się także szkła mineralne dodatkowo utwardzane;
Szkła szafirowe – produkowane są z syntetycznego szafiru o twardości zbliżonej do szafiru naturalnego, powszechnie stosowane w zegarkach wyższej klasy. Ich twardość w skali Mohsa wynosi od 7 do 9. Wysoka odporność na zarysowania. W szkłach szafirowych często stosuje się powłokę antyrefleksyjną, która redukuje refleksy świetlne, co sprawia, że szkiełko jest przejrzyste, prawie niewidoczne, a tarcza bardzo czytelna. Powłoki mogą być nakładane na wewnętrzną i zewnętrzną część szkła (lub na obie jednocześnie); powłoka antyrefleksyjna na zewnętrznej stronie szkła może ulegać zarysowaniom;
Szkła na bazie syntetycznego diamentu – produkowane głównie w zegarkach w wersji pokazowej. Z informacji zamieszczanych w prasie fachowej wynika, że pierwsza kolekcja zegarków z tymi szkłami trafiła do sprzedaży w drugiej połowie 2003 r. Twardość w skali Mohsa: 10;
Twardość szkieł zegarków określana jest w skali twardości Mohsa. W jej obrębie wyszczególniono 10 stopni na podstawie twardości 10 minerałów, licząc od najmniej twardego: talk, gips, kalcyt, fluoryt, apatyt, ortoklaz, kwarc, topaz, korund, diament.
Metody pokrywania kolorem
Metoda galwaniczna – polega na nanoszeniu na powierzchnię danego elementu równomiernej warstwy złota lub innego metalu. Proces ten zachodzi dzięki reakcji elektrochemicznej. Ze względu na porowatą strukturę metalu, naniesienie równomiernej grubości złocenia powoduje, że wierzchnia warstwa złocenia jest również porowata. Powłoki naniesione tą metodą mają twardość bardzo podobną do złota, czyli nie są zbyt twarde. Ich trwałość zależy od grubości naniesionej warstwy. Obecnie metoda ta jest stosowana niezwykle rzadko.
Metoda PVD (Physical Vapour Deposition) – polega na osadzaniu na powierzchnię elementu cząsteczek metali lub ich związków. Najczęściej stosowaną domieszką jest związek tytanu. Całość procesu odbywa się w wysokociśnieniowych komorach, w wysokiej temperaturze i tzw. atmosferze beztlenowej. Tego typu pokrycie powoduje, że wierzchnia warstwa powłoki jest gładka, zdecydowanie twardsza od złota, dzięki czemu mniej podatna na ścieranie. Szacuje się, że pokrycie PVD jest tak samo trwałe, jak 10-mikronowe złocenie metodą galwaniczną. W złoceniu PVD niemożliwe jest określenie grubości samego złocenia, gdyż złoto w tym procesie stanowi jeden ze składników.
Obecnie znanych jest kilkadziesiąt odmian i modyfikacji metod PVD. Metody PVD różnią się od siebie np. sposobem otrzymywania par osadzanych metali lub związków przez: odparowanie, sublimację, rozpylanie katodowe lub anodowe metalu lub związku, czy sposobem nanoszenia par metalu na podłoże.
Z uwagi na sposób nanoszenia par metalu na podłoże wyróżniamy np. Platerowanie Jonowe Ion Plating (IP).
Metoda IP (Ion Plating) – rodzaj metody PVD wyodrębniony z uwagi na sposób nanoszenia par metalu. Nanoszenie cząsteczek – par metalu lub związku, uzyskiwanych w dowolny sposób, ale zjonizowanych (naładowanych) bardziej, niż przy niewspomaganych metodach naparowywania; zwykle jonizacja par metalu lub związku następuje w strefie otrzymywania par. Powoduje to, iż cząsteczki metalu łatwiej i bez dodatkowego wspomagania przylegają do materiału bazowego. W metodzie IP wykorzystuje się również znacznie niższą temperaturę nakładania powłoki – ok. 180-200 °C. Zastosowanie niskiej temperatury pozwala na stosowanie metody powlekania jonowego do materiałów o niskiej temperaturze topliwości.
Wstawki złote – metoda inkrustacji – polega na zastąpieniu złocenia wstawieniem w dane miejsce elementu wykonanego ze złotej taśmy lub w całości wykonanego ze złota. W porównaniu z 20-mikronowym złoceniem metodą galwaniczną, którego grubość wynosi 0,02 mm, grubość najcieńszej ze stosowanych blaszek wynosi 0,2 mm, czyli jest 10 razy grubsza od złocenia galwanicznego. Złocenie tego typu jest o wiele bardziej trwałe, ale, niestety, o wiele droższe. Obecnie metoda ta jest stosowana bardzo rzadko.
Niezależnie od rodzaju powłoki, nie jest ona całkowicie odporna na działanie czynników zewnętrznych. Jej trwałość zależy również od specyfiki i sposobu użytkowania zegarka.